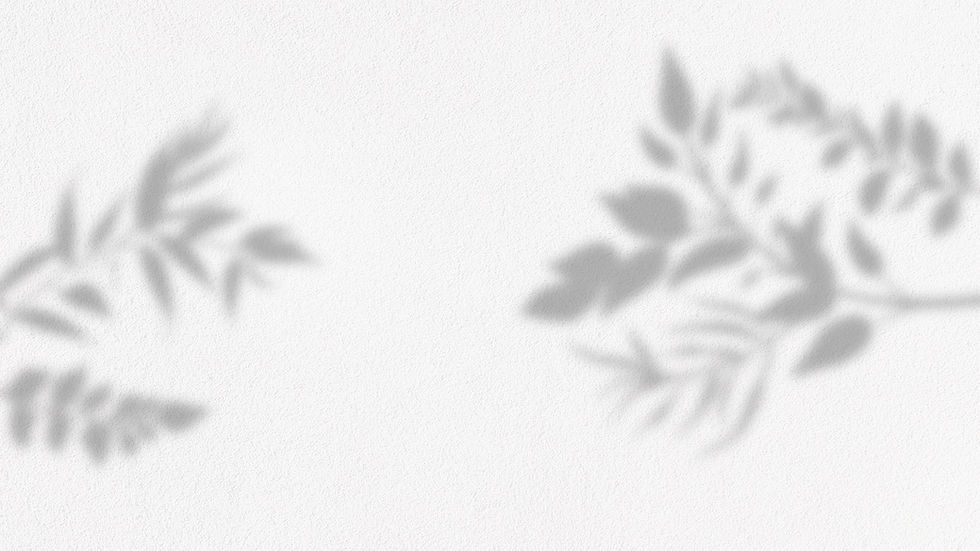
Journey
Dreaming and designing your home is a joyful journey we take along with you. We take inputs from you, understand the need and the place. Leave all your worry to us as we undertake all aspects of realisation of your dream home. Also, keep you informed at all stages of progress.
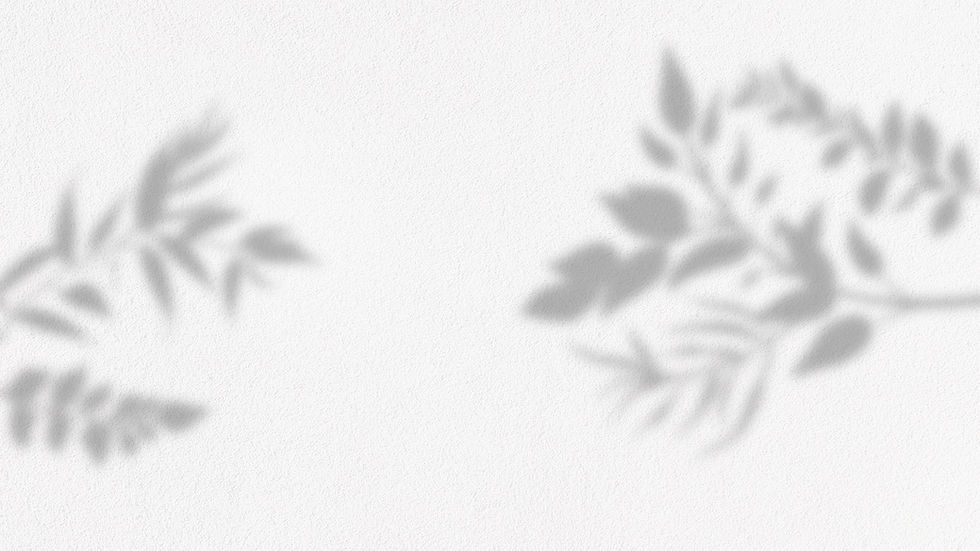
Pre Design Phase : ​

There would be lots of doubt & uncertainty before committing to an interior designer. What are the possibilities, what could be afforded, whether something would work or not.
​
Get answer to all your queries, explore what's possible and then choose once you are satisfied and ready for starting the journey.
Use this phase of exploration, sharing your stories & home aspirations with guidance & expertise of our designers.
Design Consultation
In the first stages of interior design discussions, professionals and clients work together to grasp preferences, objectives, and limitations. This involves delving into style choices, color palettes, functional needs, and budgetary constraints. These conversations lay the groundwork for tailoring a design plan to meet the client's specific requirements, culminating in an estimate for the proposed project.
Experience Center Walkthrough
Home interiors experience center walkthrough typically involves exploring various rooms and setups showcasing different furniture, fittings, decor, and design elements. Visitors can gather ideas, visualize how products might look in their own homes, and gain inspiration for interior design. It's a hands-on way to experience and choose items for enhancing home aesthetics.
Accurate Quote
We offer a transparent approach by furnishing a precise estimate upfront, enabling customers to plan their budget with confidence, devoid of hidden or additional expenses. Unlike industry practices that tend to lowball initial estimates and escalate prices during the design phase, we prioritize honesty and consistency, steering clear of trapping clients with unexpected cost hikes.
Payment Milestone
The Handshake
The handshake signifies the commencement of our partnership to bring your dream home to life. To initiate the design process and move forward, a payment equivalent to 10% of the estimated project cost is required. This step solidifies our commitment to transforming your vision into a reality.
Timely payment at this milestone allows to proceed & work on the next phase
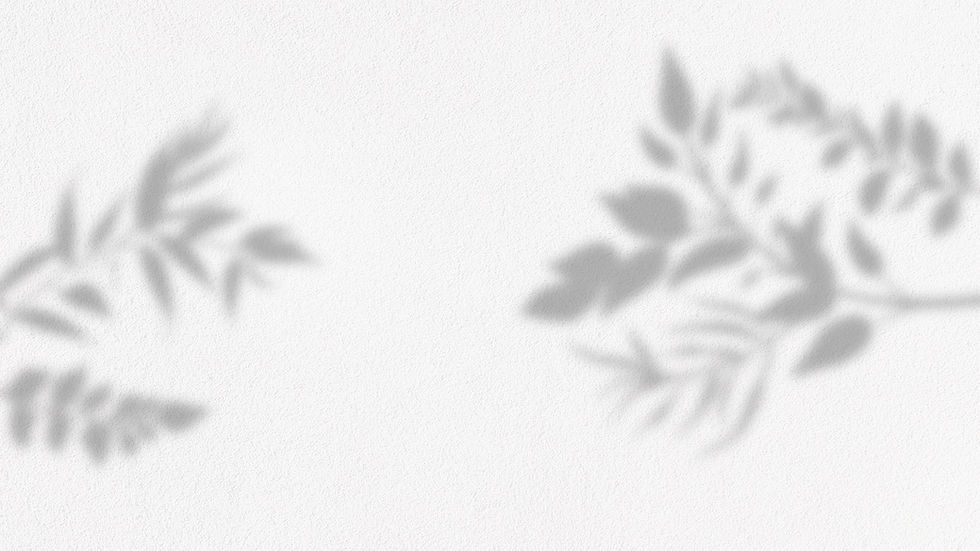
Design Phase : ​

In the design phase, all considerations for design requirements, site inspection is done & designs are prepared to suit the requirements.
It follows with review & adjustments accordingly so that once things start moving, there will be very little left to guess. This also ensures timely delivery & committing to a budget beforehand.
Site Measurements
We conduct on-site visits to your apartment, villa, or row house, capturing precise pictures, videos, and measurements of walls, windows, doors, electrical points, and more. This meticulous data collection ensures a seamless and highly accurate design process tailored to your space.
Customised Design Solutions
Customized interior design solutions involve tailoring every aspect of the design to meet the specific needs, preferences, and lifestyle of the client. This includes personalized color schemes, furniture selections, layout arrangements, and decorative elements. The goal is to create a unique and harmonious living space that aligns perfectly with the client's vision and requirements, providing a one-of-a-kind interior tailored to their individual style and functionality needs.
Design QC
Interior design quality checks are thorough evaluations conducted to ensure that the executed design aligns with the planned vision and meets predefined standards. This process involves assessing the craftsmanship, materials, and overall aesthetics of the interior elements. Quality checks help identify and rectify any discrepancies, ensuring that the final result reflects the desired design integrity, functionality, and visual appeal. It's a crucial step to guarantee client satisfaction and the successful realization of the envisioned interior.
Design Sign off
Interior design signoff from the client is the formal acknowledgment and approval of the completed design. It indicates that the client has reviewed and accepted the proposed interior, including layout, furnishings, colors, and overall aesthetics. This process typically occurs after any necessary revisions and ensures that both the designer and client are in agreement before moving forward with the implementation phase. The signoff marks a crucial point where the client expresses satisfaction with the design, giving the green light for execution.
Site Validation
Interior design site measurement validation is the process of verifying and ensuring the accuracy of the measurements taken at the site. This validation is crucial to guarantee that the dimensions of walls, windows, doors, and other structural elements align precisely with the recorded data. By cross-referencing and validating measurements, designers can avoid discrepancies and inaccuracies that might impact the success of the design implementation. This meticulous validation process enhances the overall precision of the interior design plan, contributing to a more seamless and accurate execution.
Payment Milestone
The Commitment
Commitment signifies the client's satisfaction with every aspect of the design process and readiness to initiate the production and execution phase. This commitment is solidified by a payment of 60% of the project cost, enabling the procurement of all necessary materials and hardware fittings essential for the successful implementation of the project.
Timely payment at this milestone allows to proceed & work on the next phase
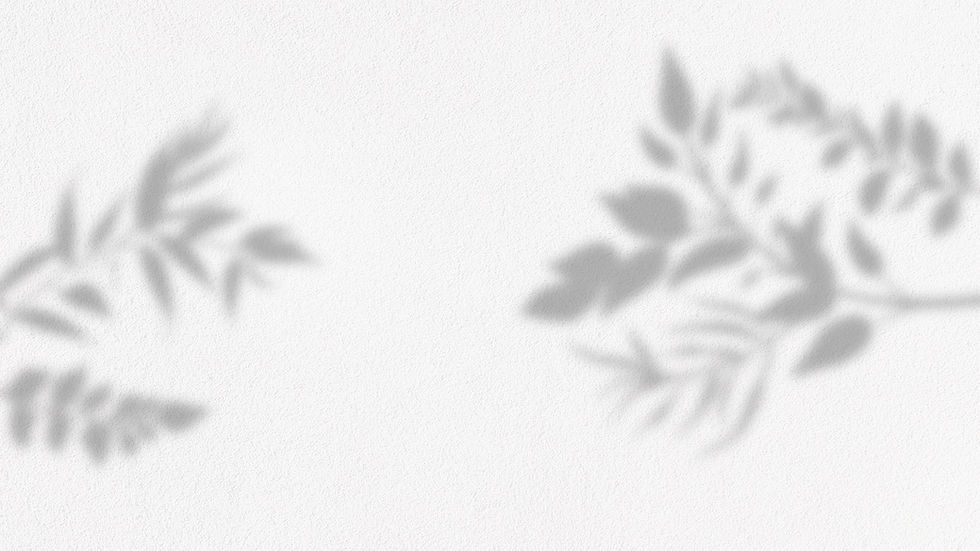

The production phase starts after design is finalised so that the manufacturing of interiors could be done fast, smoothly & precisely.
Production Phase : ​
1. Site Work Initiation
The commencement of civil, electrical, plumbing, and false ceiling work marks the beginning of the construction and installation phase in interior design. It includes -
-
Civil Work
Involves structural modifications, such as wall construction, flooring, and any alterations to the physical structure of the space.
-
Electrical Work
Encompasses the installation of electrical systems, including wiring, outlets, switches, and lighting fixtures as per the design specifications.
-
Plumbing Work
Focuses on the installation of plumbing fixtures, pipes, and connections for water supply and drainage according to the design requirements.
-
False Ceiling Work
Involves the creation and installation of false ceilings, which can enhance aesthetics, house lighting fixtures, and conceal utility lines.
This phase lays the foundation for the interior design by ensuring that the structural, electrical, plumbing, and aesthetic elements are aligned with the planned design, setting the stage for the subsequent stages of the project.
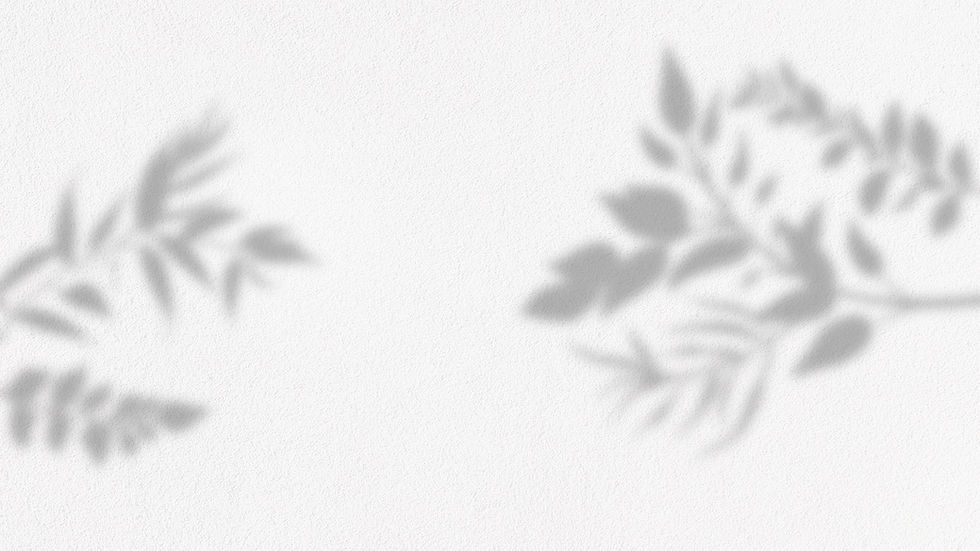
2. Production Kick Off / Onset of Manufacturing
The commencement of work in a modular furniture factory refers to the initiation of manufacturing processes for customised modular furniture pieces. This phase involves the following key activities -
-
Material Procurement
Acquiring raw materials, such as wood, metal, or other components, based on the design specifications.
-
Finishing
Applying finishes, such as paints, laminates, or veneers, to enhance the appearance and durability of the furniture.
-
Cutting and Shaping
Using precision machinery to cut and shape the materials into the required components for the furniture.
-
Assembly
Putting together the various parts and components to create the modular furniture units according to the approved design.
Commencing work in the modular furniture factory ensures that the production aligns with the approved design, maintaining quality standards and preparing the pieces for installation at the designated interior space.
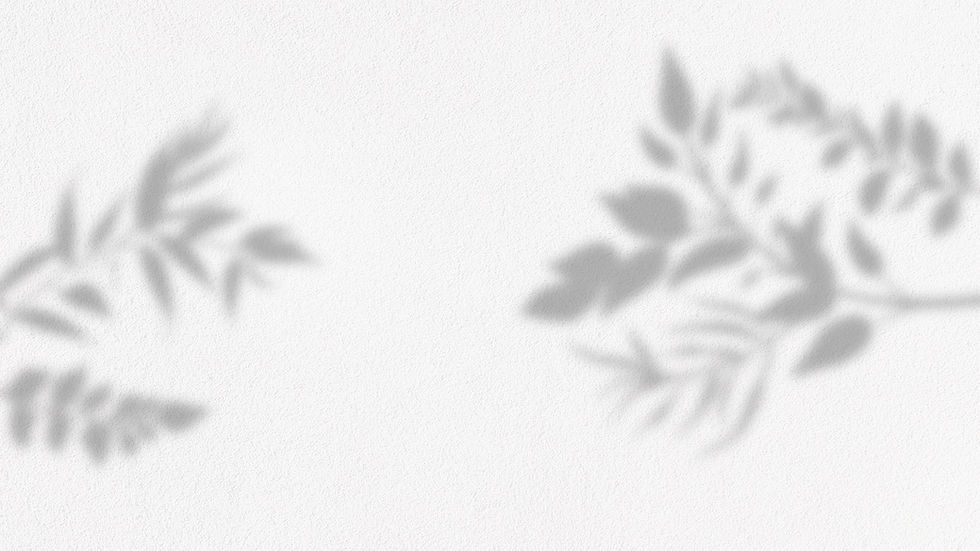
3. Pre-Assembly & QC
Production QC (Quality Control) in the context of modular furniture involves rigorous checks and evaluations throughout the manufacturing process to ensure that each piece meets predetermined quality standards. This includes -
-
Material Inspection
Verifying the quality of raw materials before production to ensure they meet specified standards.
-
Assembly Quality
Assessing the precision and accuracy of the assembly process to guarantee that all components fit together seamlessly.
-
Finish and Appearance
Examining the final appearance of the modular furniture, including finishes, colors, and overall aesthetics.
-
Functionality Checks
Testing the functionality of movable parts, drawers, doors, and any other elements to ensure smooth operation.
-
Structural Integrity
Ensuring that the modular furniture is structurally sound and meets safety standards.
Commencing work in the modular furniture factory ensures that the production aligns with the approved design, maintaining quality standards and preparing the pieces for installation at the designated interior space.
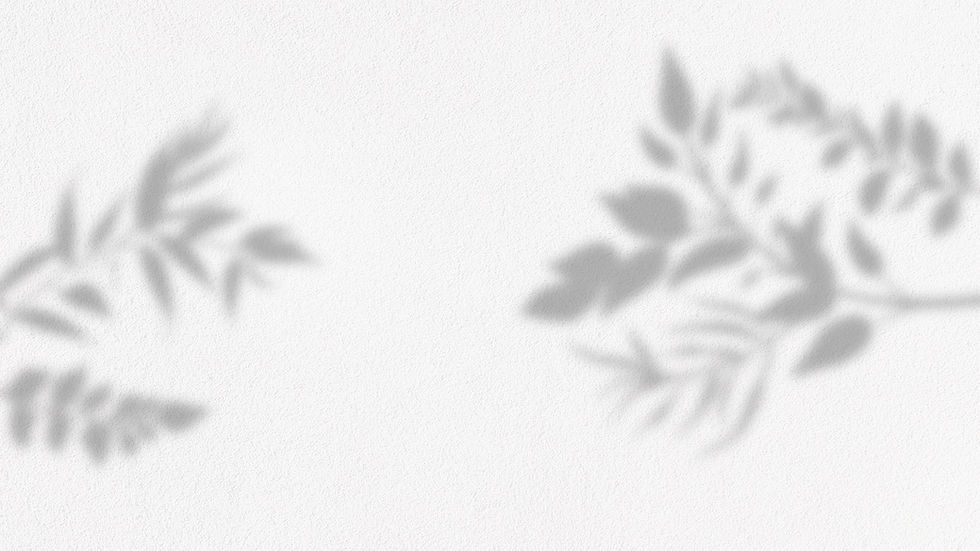
4. Production QC and packaging
The packaging process involves securely wrapping and protecting each piece of modular furniture to prevent damage during transportation. It includes -
-
Secure Wrapping
Using appropriate materials to wrap and secure individual components or entire units.
-
Cushioning
Adding protective layers, such as foam or bubble wrap, to absorb shocks and prevent scratches.
-
Labeling
Clearly labeling packages for easy identification and proper handling during transit and installation.
Production QC and packaging are integral steps to guarantee the quality, integrity, and safe delivery of modular furniture to the client's location.
Payment Milestone
The Delivery
Delivery signifies that the meticulously inspected panels and hardware have successfully passed all quality checks and are prepared for transport to the site, initiating the installation phase. To commence the delivery process, a payment of 25% of the total project cost is required. This payment ensures the smooth transition from production to on-site installation.
Timely payment at this milestone allows to proceed & work on the next phase
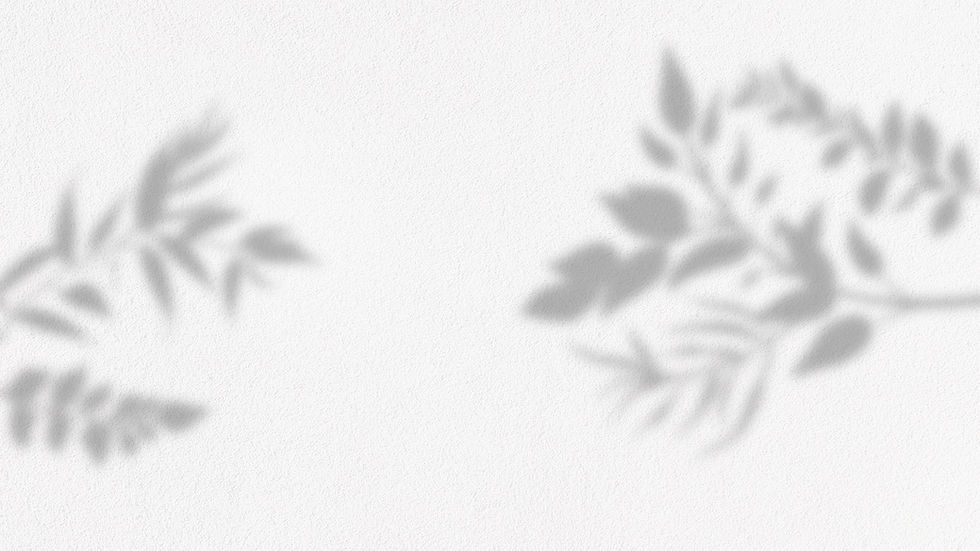
Site Implementation Starts : ​

Modular furniture installation at the site involves the on-site assembly and placement of the pre-manufactured modular components. The process includes -
-
Site Preparation
Ensuring that the designated area is ready for installation, free from obstacles or hindrances.
-
Component Layout
Placing the modular furniture components according to the approved design and layout.
-
Connection and Assembly
Joining the modular units, attaching hardware, and ensuring a secure and accurate assembly.
-
Alignment and Leveling
Ensuring that the installed furniture is aligned correctly and leveled to meet design specifications
-
Integration of Utilities
Connecting electrical components or any integrated utilities within the modular units.
-
Final Checks
Conducting a thorough inspection to verify the proper installation, alignment, and functionality of the modular furniture.
The modular furniture installation process aims to seamlessly integrate the pre-fabricated elements into the designated space, aligning with the approved design and meeting the client's expectations for both aesthetics and functionality.
Payment Milestone
The Final Payment
The final payment denotes settling the remaining 5% of the total project cost upon the completion of structuring and fixing the carcass on-site. This payment signals the transition to the final installation phase, incorporating necessary adjustments to ensure the seamless integration and functionality of the modular furniture.
Timely payment at this milestone allows to proceed & work on the next phase
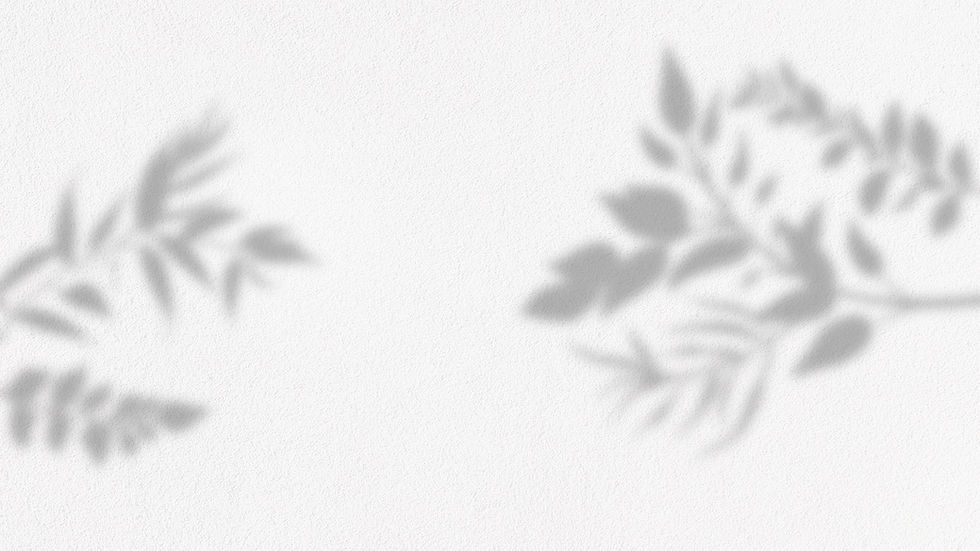
The Handover : ​

Modular furniture site QC (Quality Control) is the meticulous evaluation conducted at the installation site to ensure that the assembled modular furniture meets the expected standards and adheres to the approved design. This process includes -
1. Final QC
Modular furniture site QC (Quality Control) is the meticulous evaluation conducted at the installation site to ensure that the assembled modular furniture meets the expected standards and adheres to the approved design. This process includes -
-
Alignment and Fit
Verifying that the modular components align correctly and fit seamlessly within the designated space.
-
Functionality Checks
Testing the functionality of movable parts, drawers, doors, and any integrated features to ensure smooth operation.
-
Aesthetic Inspection
Examining the overall appearance, finishes, and details to confirm they align with the design specifications.
-
Structural Integrity
Assessing the stability and structural soundness of the installed modular furniture.
-
Utilities Integration
Confirming the proper integration of any electrical or utility components within the modular units.
Site QC is essential to identify and address any issues promptly, ensuring the successful integration of modular furniture into the intended space while meeting both design and quality standards.
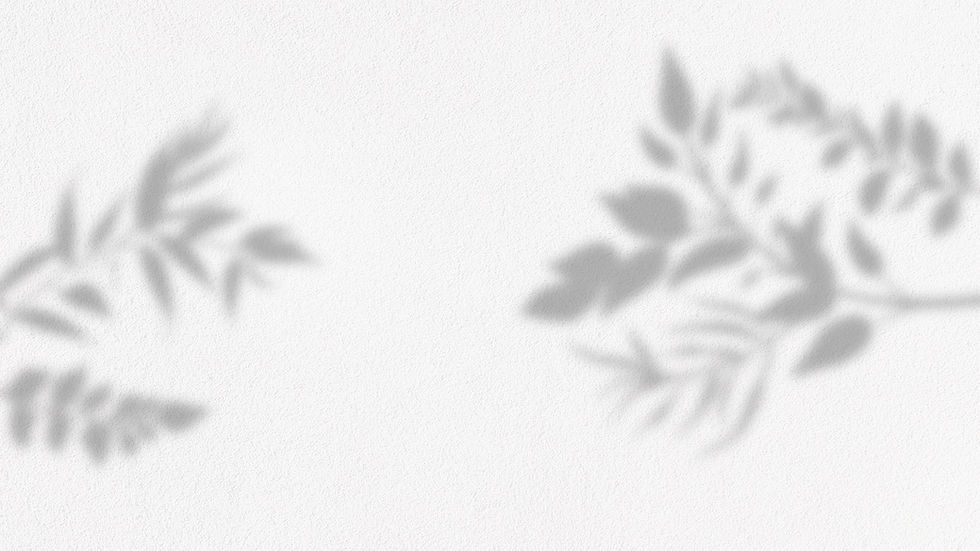
2. The Handover
The handover process in interior design is the final stage where the completed project is officially transferred to the client. This involves several key steps
-
Final Inspection
A thorough review of the entire interior space is conducted to ensure that all design elements have been implemented according to the agreed-upon specifications.
-
Client Walkthrough
The client is guided through the space to inspect and approve the finished design. Any concerns or questions are addressed during this walkthrough.
-
Documentation
Handover documents, including project plans, warranties, and maintenance guidelines, are provided to the client for their reference.
-
Demonstration of Features
If applicable, demonstrations of specific features or functionalities are given to the client, ensuring they are familiar with how to use and maintain various elements.
-
Snagging
Any minor issues or defects (snags) identified during the walkthrough are noted and addressed promptly.
-
Handover Certificate:
A formal handover certificate may be issued, signifying the completion of the project and the client's acceptance of the finished interior.
The handover process ensures a smooth transition from the design and construction phase to the client's ownership, providing them with a fully realised and functional interior space.
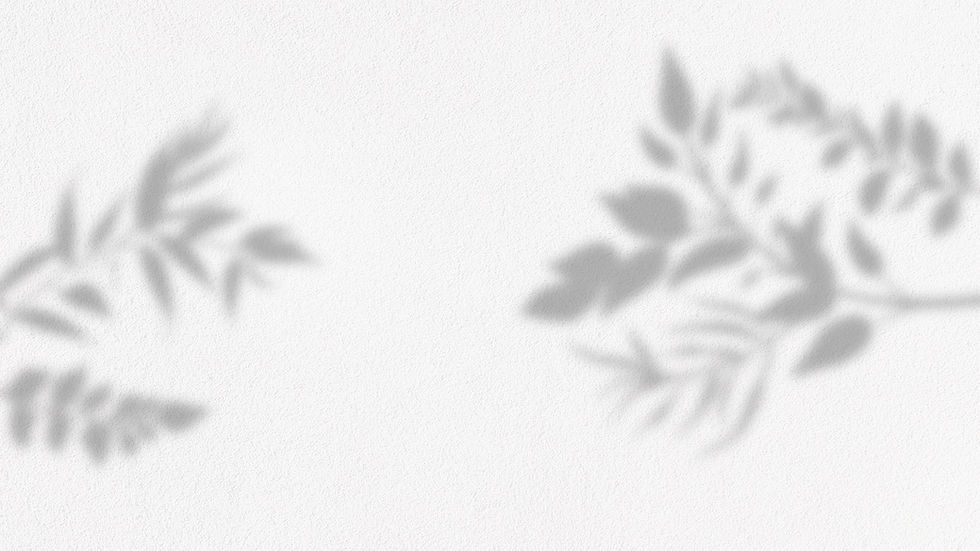
3. The Relationship Continues
The relationship continues after the handover in interior design as part of ongoing client support and satisfaction. Key aspects of this post-handover relationship include -
-
Follow-Up Communication
Regular communication to address any post-handover queries, concerns, or additional requirements the client may have.
-
Maintenance Guidance
Providing guidance on the proper maintenance and care of the implemented interior elements to ensure longevity and sustained aesthetics.
-
Warranty Support
Addressing and resolving any issues covered under warranty, ensuring client confidence in the durability and quality of the installed components.
-
Design Evolution
Supporting clients with any future design modifications or expansions, fostering an ongoing relationship as their needs and preferences evolve.
-
Feedback and Reviews
Encouraging clients to share feedback on their experience and the functionality of the design, which can be valuable for continuous improvement.
By maintaining a positive and supportive relationship post-handover, interior designers aim to ensure long-term client satisfaction and potentially foster future collaborations.